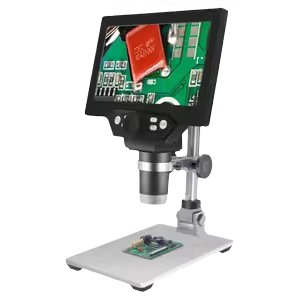
在产品研发阶段,工程师们通常会严格参照器件手册提供的标准应用电路(Reference Design)进行设计。搭建原型机时,这些电路往往表现良好,功能基本实现。然而,当产品进入批量生产并投放市场后,有时会莫名其妙地出现一些难以复现、难以定位根源的故障。这种现象令人困扰:为何在实验室验证通过的“标准”设计,到了实际应用中却变得不可靠?究其原因,通常可归结为以下四个方面:
1. 前后级匹配的隐忧
器件手册提供的标准电路,通常是基于“理想”或“典型”的前级输入特性和后级负载特性设计的。然而,我们实际应用中的电路环境,其前后级接口特性未必与手册假设的“常规状况”完全一致。这种不匹配可能引发多种问题:
* 阻抗失配: 输入/输出阻抗的不匹配会导致信号分压效应,造成信号幅度衰减或畸变。
* 互联参数限制: 前后级器件之间的相互作用(如容性负载、驱动特性)可能对数据速率、带宽或建立/保持时间产生限制,超出预期。
* 驱动能力不足: 前级器件的驱动能力(电流、电压)可能无法满足后级器件在特定工况下的实际需求(如峰值电流、容性负载充电),导致逻辑错误或性能下降。
* 负载特性变化: 后级负载(如电机、传感器、其他IC)的实际特性(阻抗、容性/感性)可能偏离手册假设的“标准”负载,影响前级工作点或稳定性。
2. 寄生参数的“暗礁”
器件手册仅提供原理图,而具体的PCB布局布线(Layout)方案则完全取决于设计工程师。不同的工程师、不同的布局布线策略,会引入千差万别的寄生参数(Parasitic Parameters):
* 走线电感: 电源线、地线、信号线本身固有的电感,在电流变化时(尤其是高频或开关瞬间)会产生感应电压(V=L*di/dt),可能导致地弹(Ground Bounce)、电源噪声或信号过冲/下冲。
* 分布电容: 平行走线、过孔、铺铜区域之间形成的分布电容,会降低信号边沿速度(增加上升/下降时间),可能造成信号延迟、串扰(Crosstalk)甚至影响高频电路的稳定性。
* 这些寄生效应在低速信号下可能微不足道,但对于高速信号、快速边沿(陡峭的上升/下降沿)信号、大电流开关路径,其负面影响会被显著放大,成为信号完整性和EMC问题的根源。
3. 瞬态过程的“脆弱时刻”
器件手册的标准电路及其性能参数,大多是基于稳态工作条件给出的。稳态测试下,电路通常表现正常。然而,实际系统运行中,各模块不可避免地经历频繁的开关切换过程(On-Off 或 Off-On):
* 瞬态冲击: 在开关切换的瞬间,电流、电压会发生剧烈变化。此时,前面提到的前后级匹配问题和寄生参数(尤其是电感效应)会急剧放大其负面作用。
* 典型案例: IGBT或功率MOSFET的栅极-发射极(Gate-Emitter)或栅极-源极(Gate-Source)击穿损坏,往往并非发生在稳态导通或关断时,而是在关断瞬间。此时,发射极/源极(E/S)路径上的布线电感(L)感应出尖峰电压(V=L*di/dt),叠加在栅极驱动信号上,极易超过栅极氧化层的薄弱耐压(Vge/Vgs rating)而导致失效。手册给出的稳态耐压值在瞬态冲击面前显得尤为不足。
4. 器件一致性的“概率陷阱”
即使电路设计完美规避了上述所有系统性风险,大规模批量生产本身也引入了新的不确定性——器件固有的一致性问题:
* 工艺波动: 半导体制造过程极其复杂且精密,微小的工艺波动在所难免。这会导致同一批次甚至同一晶圆上的不同芯片,其关键参数(阈值电压、导通电阻、增益、漏电流等)存在自然分布,部分器件可能处于规格边缘或存在微小缺陷。
* 小概率失效: 在大批量生产和漫长的使用周期中,这些处于边缘状态或存在潜在缺陷的器件,在特定的工作条件组合(温度、电压、负载、信号边沿)下,就可能暴露出问题。
* 排查困境: 这类由器件个体差异(而非设计缺陷)引发的失效,通常表现为偶发、难以复现。即使对故障件进行详尽的电路原理图、PCB布线、甚至器件结构分析,也常常无功而返,因为问题根源在于器件微观层面的个体差异。
结论:
器件手册的标准电路是宝贵的起点,但绝非确保产品最终可靠性的“保险箱”。从实验室原型到稳定量产,工程师需要深刻理解并主动应对前后级匹配的复杂性、寄生参数(尤其是Layout引入的)的潜在影响、瞬态过程的严酷性以及大规模生产带来的器件一致性挑战。成功的产品设计不仅在于“依葫芦画瓢”,更在于超越参考设计,进行全面的系统级考量、细致的信号完整性分析、充分的瞬态工况验证以及严格的量产质量控制(包括器件筛选和可靠性测试)。唯有如此,才能最大程度地规避那些“莫名其妙”的量产故障,提升产品的稳健性与市场口碑。