在本文中,您将了解如何在生产环境中组装采用表面贴装技术 (SMT) 组件的印刷电路板 (PCB)。
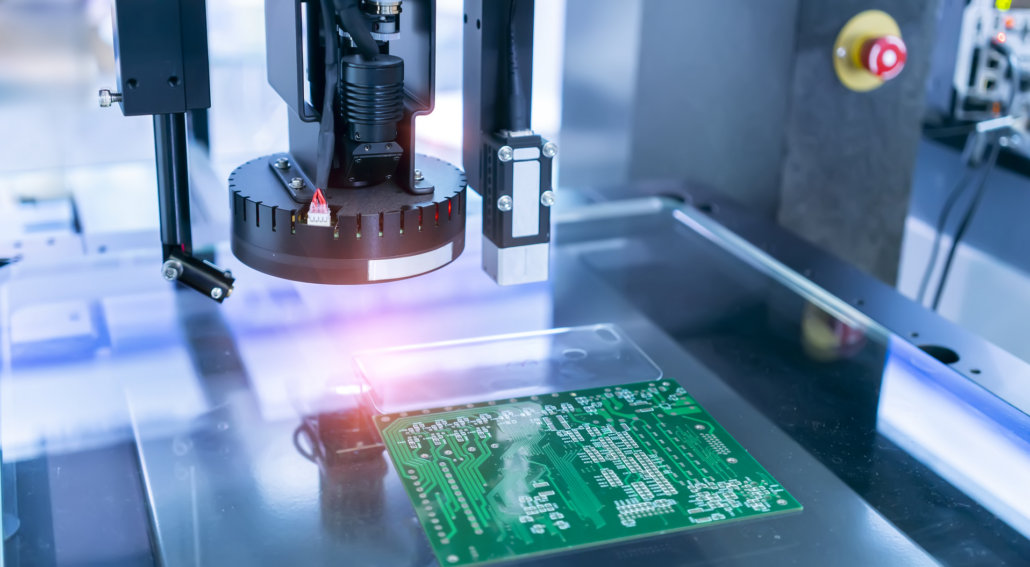
随着电子产品的小型化和对更智能、更易于使用和更精确技术的需求,表面贴装技术 (SMT) 成为 1980 年代初期印刷电路板组装 (PCBA) 的首选技术。
在表面贴装技术流行之前,通孔技术是一种主流技术,将元件引线(轴向或径向样式)插入裸 PCB 上的孔,然后进行焊接。
电路板的一侧称为“组件侧”,另一侧称为“焊接侧”,这一术语至今仍在使用。
即使在今天,这两种技术仍在使用中,甚至可以在同一块板上共存,都具有各自的优势。
由于通孔技术可实现更牢固的物理连接,因此它被认为是设计高可靠性产品的更好方法,适用于可承受环境压力的坚固甚至商业应用。
对于可能因质量而承受机械应力(即振动)的组件(例如连接器)或较大的组件(例如去耦电容器、变压器等),它也是一个很好的选择。
表面贴装技术,最初称为平面贴装,是一种使用扁平引线或小金属焊盘将电子元件安装到印刷电路板表面的方法。
当需要大批量 PCB 或需要小型化以满足独特要求时,这种技术很有帮助。
与通孔技术不同,表面贴装允许在限制范围内方便地将组件安装在电路板的两侧,因为 SMT 技术需要通孔在电路板层之间建立连接。
图 1:带有通孔元件、表面贴装元件和过孔的电路板
当今的多层 SMT PCB 叠层从 2 层到 32 层不等,最常见的是使用 4 层和 6 层。
在这种情况下,表面贴装技术的优势在于通过增加每平方英寸 PCB 的连接数来进一步减小 PCB 的尺寸。
为了更好地了解复杂程度,让我们看一下 PCB 叠层的内部。
图 2:PCB 叠层
请注意,图 2 中的 PCB 由几层组成。这种材料排列称为“PCB 叠层”,可根据 PCB 要求而有所不同。
叠层的两个关键组成部分是铜箔层——用于导电——和层压层——提供结构和绝缘。
铜箔层被“蚀刻”以绘制特定的布线图案,并且厚度可以变化:较厚的层允许更多的电流流动。
使用的标准铜厚度为 1 盎司。有趣的是,PCB 生产中的铜厚度以盎司 (oz.) 为单位测量,其中将特定重量的铜铺展到 1 平方英尺(等于 1.37 密耳或 0.0348 毫米)。
此外,1.5 盎司和 2 盎司也是标准铜厚度,这将允许相应地更高的电流在电路中流动。
层压层由纤维增强环氧树脂组成。它们有两种基本类型:“Cores”,有预固化的铜箔,以及“PrePreg”,没有铜箔,环氧树脂没有完全固化。
当叠层通过压力和热量组装和固化时,PrePreg 层充当将所有层粘合在一起的胶水。
图 3:柔性 PCB
PCB 制造中最常见的层压板类型称为“FR4”,但不同的层压板(BT 环氧树脂、聚酰亚胺、特氟龙等)可用于要求更高的应用,例如高频或高温。
同时,有不同类型的PCB:刚性、柔性和刚性-柔性。刚性多氯联苯是更传统的多氯联苯,顾名思义,本质上是刚性的或不灵活的。
柔性 PCB 是通过用薄聚酰亚胺层代替核心或预浸层来构建的,聚酰亚胺层可以弯曲或成形以适应空间限制要求。
由于可穿戴设备的小型化和普及,如今柔性 PCB 正变得越来越主流。
另一方面,刚柔结合是刚性和柔性PCB的组合,结合了柔性电路的多功能性和刚性PCB的稳定性。
通过消除对连接器和电缆的需求,提高了板间连接的可靠性,这是一个更可靠的系统。
它是最昂贵的 PCB 类型,主要用于航空航天或军事应用。
图 4:Flex-Rigid PCB
此外,层压板有多种厚度,允许各种叠层配置、PCB 厚度和 PCB 类型。
刚性 PCB 上所有层压板总厚度的标准选项范围为 0.2 毫米至 3.2 毫米(0.008 英寸至 0.240 英寸)。
最常见的选项包括 0.8 毫米(0.032 英寸)、1.6 毫米(0.063 英寸)和 3.175 毫米(0.125 英寸)。
虽然普通板在此范围内,但背板往往更厚,接近该范围的末端以增加机械强度。
另一方面,我们有很薄(0.065 毫米至 0.42 毫米)且高度灵活的柔性 PCB。
PCB 通常将其外部铜层覆盖在一层薄薄的“阻焊层”中,以保护铜免受腐蚀并充当绝缘体,仅暴露焊盘。
大多数情况下,阻焊层是绿色的,但也可以是红色、蓝色、黑色、红色、白色等。
图 5:带有彩色阻焊层的 PCBS
在阻焊层上,PCB上呈现出一层称为丝印的铭文。
丝印是一层墨水痕迹,在 PCB 上标记文本和符号,以识别组件的位置(基于参考指示符)并指定组件的方向。
提醒一句:重要的是要避免焊盘上的丝印重叠,如图 6 所示,因为它们会在焊接过程中产生问题,从长远来看可能会造成灾难性后果。
图 6:丝印重叠
当今使用的焊盘最常见的表面处理是:热风焊料水平 (HASL)、无铅 HASL、浸银 (Au)、浸锡 (Sn)、化学镀镍浸金 (ENIG) 和化学镀镍钯浸金(ENEPIG)。这些是从最低到最昂贵的技术列出的。
简而言之,更好的表面处理为焊盘提供了更直的表面,从而可以更好地焊接焊盘上的组件。
ENIG 是久经考验的行业标准,大多数 PCB 制造商都可以轻松获得。ENIG 沉积物具有更紧密、更均匀的晶粒并保持高可焊性,同时还耐腐蚀。
当今最常用的叠层是具有 ENIG 涂层和绿色阻焊层的 4 层叠层,其中两个中间层专用于“电源”(VCC 或 VCC 值的多个组合)和“接地”(GND)。
其余的外层用于组件之间的连接。
现在我们对 PCB 技术有了一个总体了解,让我们回顾一下 PCB 组装过程中涉及的各个步骤。
PCB 前组装
印刷电路板设计
电子设计师将功能要求转化为“示意图”——象征性的配方,显示将使用哪些电子元件以及如何连接它们以构成功能电路。
原理图被抽象为包含电路的概念信息。然后将原理图“配方”转变为“PCB布局”——一组图纸,以可以制造的方式显示电子元件的物理方面及其连接。
布局包括每个铜层的二维图、钻孔(通孔)信息、叠层信息、质量标准要求和最终电路板的 3 维模型。
设计人员使用计算机辅助设计 (CAD) 软件来执行设计规则并执行自动检查,以使最终结果与原理图的规格相匹配并满足制造要求。
CAD 软件用于将设计转换为电路板制造厂(Gerber 文件)和装配厂(拾放文件和/或装配文件)的文件。
在此之后,进行验证过程(设计规则检查)以确定任何布局错误,以免影响电路板功能或制造能力。
该设计通过 DFM(制造设计)和 DFA(装配设计)检查质量、准确性、模块化和一致性。
PCB制造
完成设计验证后,需要准备制造文件,其中包含 PCB 制造商普遍接受的样式和格式的信息。
制造文件包括特定格式的 Gerber 文件、网表、制造图、装配图、NC 钻孔文件、盲孔/埋孔信息、材料清单和 PCB 面板图。
图 7:防潮袋 (MBB)
准备 PCB 和组件
一旦制造出 PCBA 并购买了组件,就需要为组装目的做好准备。
回流组装的准备步骤之一是确保 PCBA 和组件都具有低湿度。
PCB 和对湿气敏感的组件必须在组装前进行烘烤,以使其干燥。
PCBA 和元件烘烤是在温控烘箱中进行的过程,烘烤的温度和时间取决于 PCB 和元件的厚度和暴露(标准 J-STD-033)。
典型的烘烤温度范围从 125 摄氏度到 150 摄氏度,可以持续 24 小时。PCB Baking 避免了电路板上存在水分时可能发生的 IC 爆裂和 PCB 分层等问题。
湿气敏感部件必须真空密封在带有干燥剂(图 9)和湿度指示卡(图 10)的防潮袋(图 7)中,并且只能在组装前从袋中取出。
移除后,有一个 168 小时的窗口来执行回流工艺(对于 MSL3 组件)。超过这一点,组件必须重新烘烤以用于组装或存储目的。
图8:密封真空机
图 9:干燥剂
图 10:湿度指示卡 (HIC)
准备 PCB 组装
在组装之前,需要完成一些准备工作以确保成功的生产运行。
根据制造文件,工程师必须准备工作说明、确定程序并创建数据日志。
在丝网印刷的情况下,准备模板是一个重要的步骤。正如该术语所暗示的那样,模板是具有与 PCB 上的组件焊盘相对应的孔的薄片材料。
每个 PCB 都需要一个独特的模板,这种焊膏应用方法在大批量生产中特别有用。我将在下一节中对此进行更多讨论。
接下来,必须为每个产品准备机器程序。编程是根据安装位置信息、PCB 的长度、宽度和厚度、材料信息等来完成的。
一种选择是在生产线处理前一次运行时离线进行此准备工作。机器程序设置为离线,以便在不浪费时间的情况下快速加载下一次运行。
在特殊应用的情况下,需要提前确定和计划先决条件。
例如,对于柔性 PCB,重要的是要考虑一个 SMT 托盘,它有助于通过 SMT 工艺支撑和运输柔性 PCB。
PCB组装
锡膏应用
制造的电路板最初通过指定焊盘上的焊膏应用。
焊膏是金属焊料颗粒和助焊剂的组合,有助于清洁焊接表面的杂质和氧化。它还用作将电子元件粘合到印刷电路板上的粘合剂。
焊膏应用可以通过模板丝网印刷焊膏或通过更先进的非接触式喷射印刷方法完成。一旦应用,模板必须清洁并用于下一块板。
对于每一个新设计,都必须制造一个新的模板,这可能非常昂贵,尤其是在中低生产水平的情况下。
另一方面,喷射印刷是一种非接触式方法,可在每个表面贴装焊盘上沉积准确数量的焊料,并允许每小时约 40,000 个焊盘施加焊料,点胶速度超过每小时 100 万点.
该技术通过应用单个点来增加焊膏体积,从而为每个组件实现正确的用量。
喷射印刷更适合特殊应用,例如针入膏、腔中粘贴等,其中 PCBA 的 3D 特征无法通过 2D 技术(模板应用)提供服务。
尽管喷射印刷因其提供的固有优势而获得了很大的动力,例如更快的转换和不需要模板,但在大批量生产的情况下,基于模板的丝网印刷仍然是焊膏应用的首选方法。
对于大型和非常小型组件混合的设计,在一个设置中应用适量的焊料是一项挑战,丝网印刷与喷射印刷相结合是一种理想的解决方案。
应用焊膏后,必须对较重的组件进行特殊考虑。通常,较重的组件将在回流工艺的第二道工序中进行焊接。
但是,如果它们最终位于板的底部,第二次通过烤箱,则必须将它们粘在适当的位置以避免由于重力而移位。
为了完成,在元件放置之前,根据较大元件的位置(手动/自动)添加 SMT 粘合剂滴。
锡膏检查
在通过任一方法涂敷锡膏后,对于大批量要求,进行焊膏检查 (SPI) 以确保焊膏沉积的对齐、数量和质量。
不正确的焊膏印刷会导致焊点缺陷,从而导致废品。过多的焊膏会导致短路和桥接,而焊膏不足则不会产生所需的电气连接。
拾取和放置组件
应用焊膏后,下一步是将组件放置在焊点上。
对于 SMT 技术,此过程由拾放机处理,这些机器可以高速、高精度地放置各种电子元件,如电容器、电阻器、IC 等。
表面贴装元件以卷带或托盘形式提供给机器,这些卷带或托盘装载到安装在拾取和放置机器上的供料器上。
图 11:卷带包装中的元件(电阻器)
根据 PCB 设计文件,拾放机将使用真空吸管、气动吸盘或夹具从托盘或卷轴中拾取每个组件(具有预编程的 XY 坐标和旋转),并将其小心地放置在精确的焊料上在板上粘贴应用位置。
如今,最快的贴装机提供高达 250,000 CPH(每小时元件数)的贴装速度,可优化几台 PnP 机器的组合。
在此阶段将检查组件放置精度、完整性、方向和极性。
回流焊接
一旦组件就位,它们必须被焊接以牢固地连接到接触垫上。在此过程中,PCB 被移入回流炉,焊膏在此熔化并在高温下粘合组件和触点,从而形成焊点。
小型化 PCBA 在焊接过程中使用氮气惰性化气氛已成为常见做法。氮基回流焊环境可最大限度地减少焊接表面氧化的机会。
更长的回流炉将有更多的温度区域,这将允许区域之间的温度过渡更平滑,从而重新创建推荐的焊料曲线并获得更好的结果。
标准回流炉有四个温度区(见下图):
- 预热区:焊膏在此温度下被激活。
- 吸收/热浸泡区:各种组件的温度稳定在这个温度。
- 回流区:该区域的温度最高,是焊膏完全熔化的时候。这个区域的时间应该更短,否则可能会损坏PCB/组件。
- 冷却区:温度冷却到焊膏凝固点以下,使焊点凝固。
图 12:回流炉中的温度区(图片来源)
这些区域的温度必须始终控制在适当的范围内,以避免损坏组件和焊接/焊接质量。
值得一提的是,如今,由于其对环境和健康的负面影响,几乎所有铅焊料都将被淘汰,并且更常用的是符合 RoHS 标准的无铅焊料。
此步骤完成 PCB 组装过程。
PCBA后质量控制
人工检查
虽然不是最可靠的检查方法,但我们在这里提到这一点,因为电路板需要在组装过程的每一步由 PCBA 技术人员手动检查。
这对于组件密度较低的电路板尤其可行,并且对于高级 SMT 电路板可能具有挑战性。
自动光学检测
AOI 方法使用安装在不同角度的多个高分辨率相机来检测电路板缺陷和焊接缺陷。AOI 成像技术已从 2D(用于简单的检查、测量或方向检测)发展为可提供精确数据的 3D 成像。
这种检查方法可以检测电路板缺陷,例如错误/缺失的零件、不正确的方向和极性以及倾斜(在行业中称为墓碑)或翻转的组件。
它还可以检测焊料缺陷,例如无焊料/焊料不足、焊料过多或焊桥。
尽管 3D 成像很受欢迎,但 AOI 系统在同时采用 2D 和 3D 检测技术时效率更高。
X 射线检测
X-Ray 检测一般用于测试复杂高密度芯片的 PCB 焊接质量和精度,在无法应用光学检测的情况下。
应用时,X 射线可以确定焊料的精确程度,并可以检测隐藏在 IC 封装下的缺陷。
检测到的缺陷包括过多的焊料(焊料、桥接)、焊点开路、引脚翘起和接头错位等。
它是 BGA 等高密度组件的首选检测方法,因为该技术可以让您看到 PCB 组件的“内部”。
测试
在 PCB 组装之后,最终的 PCB 应由 QC 工程师进行测试,以确定任何问题或缺陷。
主要有两种类型的测试,飞针测试和测试夹具。飞针是小批量、关键应用 PCBA(军事、运输、航空航天)的首选测试方法。
该测试涉及使用多个电探针,它们自动与电路板接触,并应用于电路板。有些提供外部刺激,有些读取董事会的反应。
计划测试、对机器进行编程和执行测试是一个非常需要工程的过程。飞针机通常非常昂贵,通常首选用于测试针对关键应用的 PCBA。
对于批量生产,测试夹具是更好的选择。它们是针对独特 PCBA 的专用或定制测试平台。使用静态探头,将电信号和电源施加到 PCB 上,并检查和测量输出。
该测试将确保 PCB 满足设计中指定的电气要求。测试可能需要几秒钟到几分钟。
除了测试之外,在这个阶段也可以将最终的生产固件加载到板上。
准备
测试后,使用超声波清洗方法清洗电路板,目的是洗掉在组装过程中可能积聚的任何助焊剂、树脂或焊料残留物、灰尘或污垢。
清洁后,电路板准备好进行保形涂层,在电路板上涂上一层薄薄的保护涂层材料,以防止水分污染、腐蚀、氧化等。
它可以保护 PCB 免受机械振动、热冲击和其他不利环境条件的影响。
最后,PCBA 现在可以进行包装和运输了。PCBA通常包装在防静电袋中。
图 13:要包装在防静电袋中的 PCB
装配设计
不提及装配设计原则就结束这篇博客是不明智的。
我们知道以制造、组装、成本、可靠性、可测试性、可服务性、供应链、法规遵从性、创新、可回收性等为愿景进行设计的重要性。
对于 PCBA,如果最初的 PCBA 设计只关注电路板,而没有考虑应用、用例或系统环境,那么该 PCBA 就无法进行组装设计。
单独来看,PCBA 设计可能是完美的,但还有其他问题需要考虑 – 是否有可用于生产订单的组件,正在使用的组件的尺寸和数量是多少,它们是否适合大批量生产?
装配设计 (DFA) 的主要目标是消除复杂性并减少不确定性,同时提高效率。
考虑到这一原则,我们鼓励设计师从大局出发,并在每个阶段考虑设计含义。
设计师做出的 PCBA 设计决策不仅会影响 PCBA 的组装,还会直接影响到成品的形式、质量和可靠性。